NgVideoHero
JSS component is missing React implementation. See the developer console for more information.
When a government defense agency decides to procure new missile systems, they are faced with a set of design challenges. They must first define a complex, interrelated set of mission requirements — from the missile's intended targets to how it will be launched (e.g., from a plane in flight, a ship or a mobile ground launcher) — and everything in between.
Once the mission is defined, the contractor building the system must meet those requirements by packaging together the suitable warhead, guidance and control units, and propulsion systems in the missile. Constraints on size, weight and configuration may be extremely strict, especially for air-launched missiles and other launch environments.
Faced with these complexities, as well as concerns about cost and development time, there can be a strong temptation for both the customer and contractor to go with commercial off-the-shelf (COTS) component systems. A major benefit of COTS is, since they are already proven to work in certain scenarios, there is less development time and it can be easier to insert new technology. The customer can simply ask the prime contractor to package those components into a missile airframe — or so it seems.
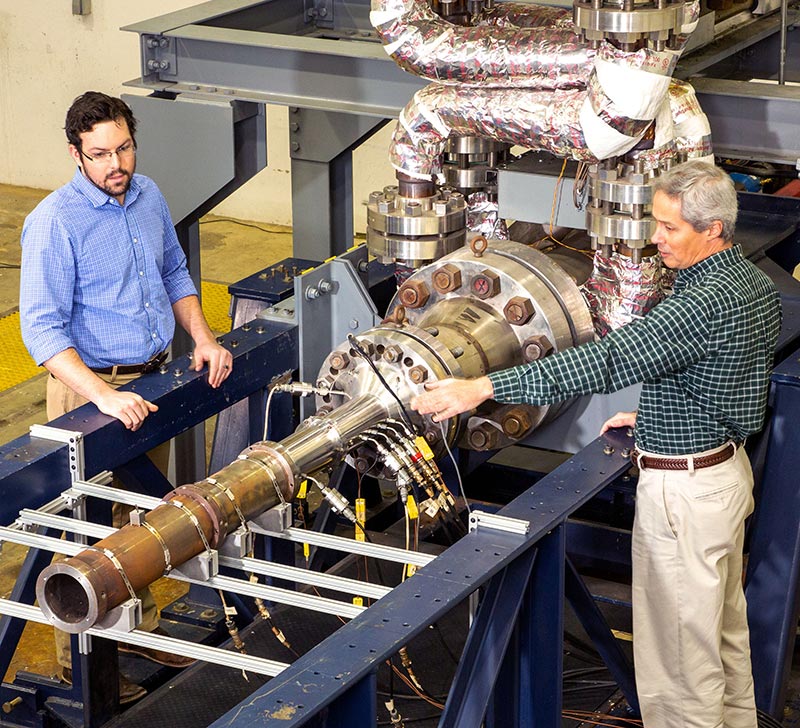
The Challenge of Integrating Complexity
An everyday example proves the point: A lot of us end up needing to use two remotes to watch TV. A smart TV comes with one remote, while a streaming service may provide another. Unless they can “talk” to each other — and mostly, they can’t — we end up having to go back and forth between both. This is awkward but acceptable on the living room couch; it is not acceptable for an air defense system.
In theory, this approach of relying on specified subsystems all packaged together promises cost-effectiveness. It has powerful appeal to those who pay the bills. But in practice, it is all too likely to deliver a missile with needlessly limited capabilities, and experience has shown that, in nearly all cases, missiles that hit their targets are far more cost-effective than those that fall short.
The problem, according to Chuck Johnson, Vice President of Northrop Grumman’s missile products, is that there are many requirements that go into designing a missile. These include platform integration, launch conditions, size, weight and power (SWAP) requirements, range, time to target, survivability, lethality, and more.
All these requirements create very tight constraints. As a result, Johnson says it’s easy to run into the following situation: “As the prime contractor decomposes these requirements and allocates them to each of the major components and makes decision on their approach/solution, they often unintentionally constrain (sub-optimize) individual components.”
Why does this happen?
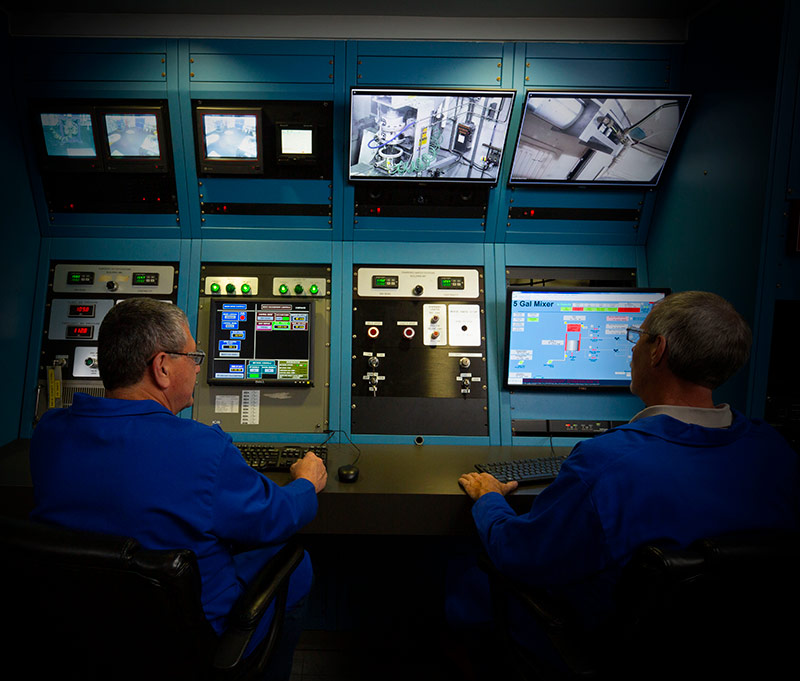
Lessons from Space
Northrop Grumman solves the integration problem by bringing best-of-breed teams together under one roof, where they can talk to each other at each stage of the design process, tweaking subsystem characteristics to achieve the optimum fit with the capabilities of other systems and the mission requirements of the complete missile.
Complex missile components, such as guidance and propulsion systems, embody a host of engineering assumptions and models devised by their individual design teams to represent the environment in which the missile will operate.
The guidance system needs to “know” the tactical geometry of the missile’s attack mission. Thus, it must incorporate a running internal representation of missile and target vectors. A propulsion system may also need an internal representation of tactical geometry to optimize the trade-off of thrust versus remaining burn time. Even the warhead, if it has more than a simple proximity fuse, might need to know the target orientation for optimum effectiveness.
If the prime contractor is simply buying these systems off the shelf to package into a missile, each system will have its own internal representation, chosen by its engineering team to meet their requirements. But these representations will not be the same, because different engineering teams may come up with different solutions to meet specific needs.
The customer then ends up having to make these differing representations “talk” to each other, and the chances for error — and resulting failure — are high.
The Power of Communication
As Johnson explains, "If you make a decision without considering the system as a whole, you will introduce design inefficiencies often unknowingly. Alternatively said, without a truly integrated team from tip to tail, you will fail to maximize the potential and create a solution that best balances the requirements and constraints."
Northrop Grumman’s solution of bringing teams together to work on these problems provides the more complete integration that these systems require.
Media Contact
Anne Eisele
703-996-6658