Foiling Failure: the Value of Forensic Science in Aerospace Engineering
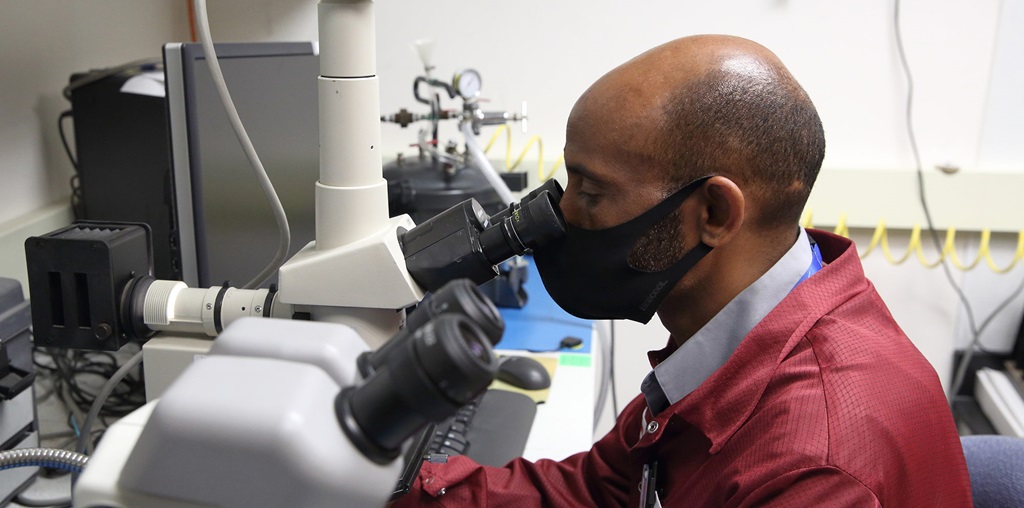
By Doug Bonderud
In our personal lives, failure offers growth opportunities. In aerospace engineering, failure puts missions and lives at risk — even a minuscule crack or poorly soldered electrical connection could doom an otherwise healthy spacecraft.
Northrop Grumman takes a proactive approach to foiling future failures through the work of specialized forensic science teams in Reliability Analysis Labs (RALs). From analyses of past failures to "destructive analyses," which test materials before they make it to orbit, RALs support customers' mission success and reduce their total risk.
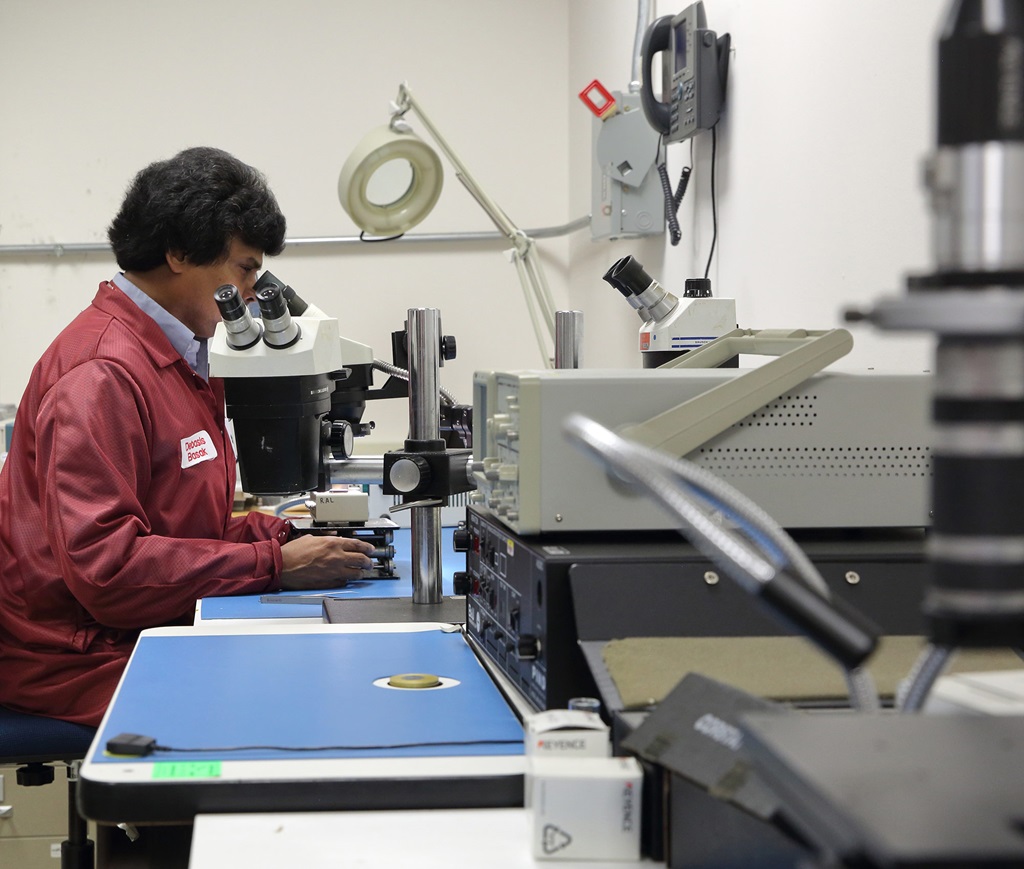
CSI: Engineering
While RAL teams have some differences from the TV series CSI, there's no shortage of engineers in lab coats peering into microscopes — but they're studying the guts of spacecraft, not people.
Because of our agile approach, we are testing repeatedly, and have a “fix” mentality when failure happens— and when it does, RALs are on the case. Using highly advanced digital microscopes, they analyze potential failure points and determine likely causes. These digital solutions allow engineers and scientists to create crystal-clear visuals in real time at extremely high levels of magnification that simply aren't possible with conventional optical microscopes.
Basak supports the Dulles, Virginia, RAL — one of more than half a dozen similar Northrop Grumman space-focused labs spread across the country. Led by an innovative team, the Dulles facility plays a critical role in discovering the key compromise points of past failures to help avoid worst-case aerospace scenarios in the future.
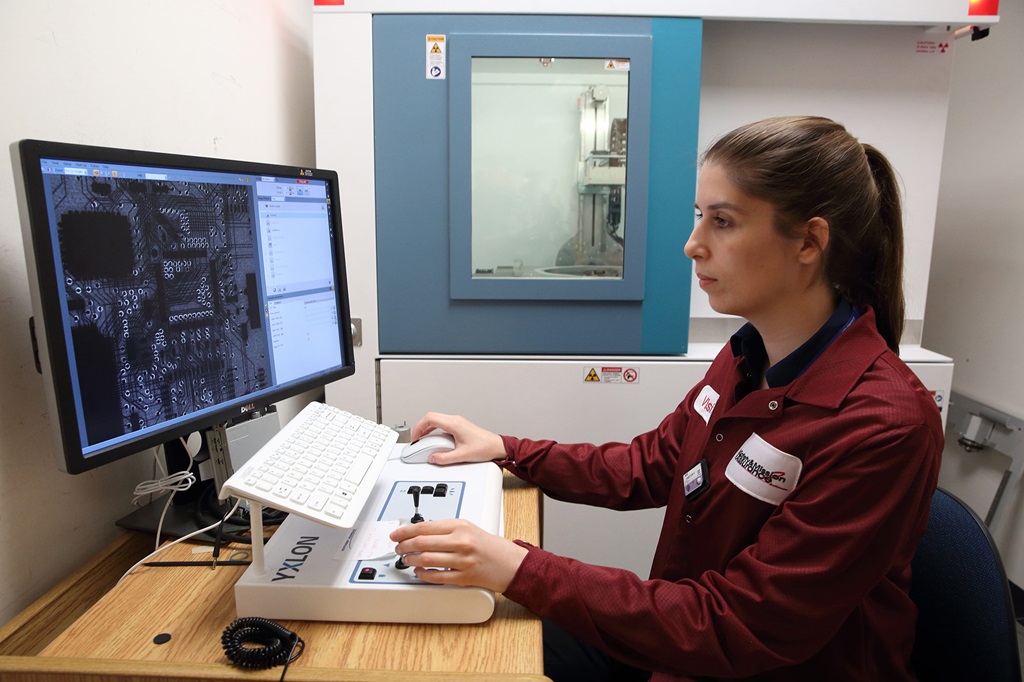
Changing the Game
Luis Ponce, a Northrop Grumman Chief Engineer, founded the Dulles RAL 40 years ago as a home base for this critical work. Along with improving mission outcomes, the facility also fosters radical transformations both in technology development and engineering expertise.
"There is no one way to approach failure analysis, so our work in the lab has always been inherently transformational," says Ponce. "Every new team member has brought new ideas, and enhanced technology has driven thousands of changes over time."
As forensic science has improved, processes executed in RALs have become more efficient, eventually doubling overall capacity and capabilities. For Ponce, there's no better example of evolving technology than the lab's original microscope — which holds a place of pride in his office — compared with the real-time frame stitching now offered by current digital solutions.
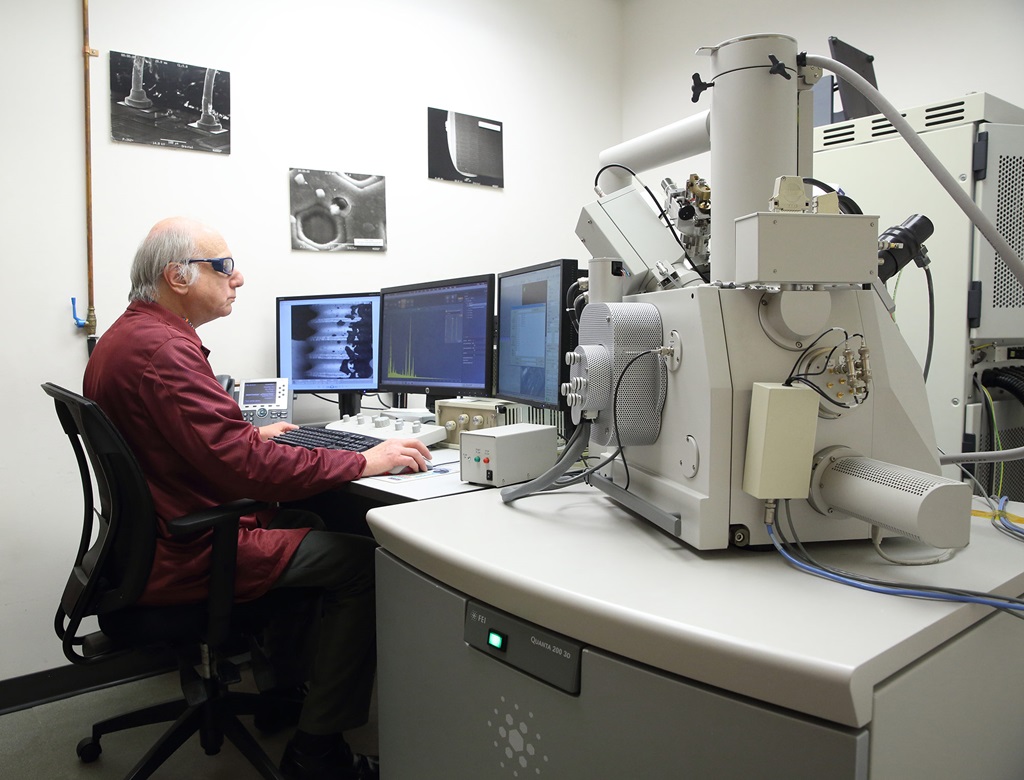
3D Scanning and Visualization Fight Failure
Combating failure on a microscopic level in the lab leads to success on orbit. Today, live X-rays allow for on-demand review of internal spacecraft structures, while enhanced microscopes — paired with 3D imaging technology — empower RAL engineers to check the accuracy and efficacy of every last electrical connection.
The Dulles RAL team is also pursuing the next level of digital inspection technology with the purchase of a Wide Area 3D Scanning and Visualization System. The system scans a microscopic spacecraft part, then creates a larger 3D model that allows engineers to see and feel its characteristics and perform rapid comparisons to identify defective parts. In effect, it's a miniature, tactile representation of potential failure points that lets RAL teams go hands-on rather than eyes only.
Digital Transformation Leads Success
According to Anthony Austin, director of safety and mission assurance, digital transformation is critical to the lab's ongoing success. "We are able to best serve programs by staying on the cutting edge of available technology," says Austin. "Enhanced 3D inspections and more accurate measurements could make all the difference in preventing future failures."
More Innovation Stories
Read all stories about advanced technology and innovation >>